There’s No Better Choice In Franklin Lakes, NJ For Expert HVAC Service
Since 1990, New Jerseyites living in Franklin Lakes have known there is only one phone call they need to make to handle all of their heating and cooling needs – Climate Plus. Our technicians are the best in the business, our tools are state-of-the-art and our commitment to quality work is unmatched. Add all that up, and the choice is clear. Whether you’re looking for HVAC repair, HVAC installation, HVAC maintenance or improved indoor air quality, we’ve got your back, front, sides, top and bottom.
Explore the links below to check out reviews from your neighbors in Franklin Lakes, NJ and the surrounding areas to see what they have to say about our service – after all, our clients are always our best cheerleaders. Then when your furnace is on the fritz, or you need a new central AC, you’ll know there’s only one name you need to remember – Climate Plus.
Recent Jobs and Reviews in Franklin Lakes, NJ
Our Local Reviews by City
- Allendale, NJ (3)
- Belleville, NJ (1)
- Berkeley Township, NJ (1)
- Bloomfield, NJ (1)
- Bloomingdale, NJ (1)
- Butler, NJ (4)
- Caldwell, NJ (1)
- Cedar Grove, NJ (3)
- Chatham Township, NJ (1)
- Clifton, NJ (7)
- Closter, NJ (1)
- Denville, NJ (1)
- Dumont, NJ (1)
- Emerson, NJ (1)
- Englewood, NJ (1)
- Englewood Cliffs, NJ (1)
- Fair Lawn, NJ (3)
- Fairfield, NJ (2)
- Fort Lee, NJ (1)
- Franklin, NJ (1)
- Franklin Lakes, NJ (2)
- Glen Ridge, NJ (1)
- Glen Rock, NJ (10)
- Guttenberg, NJ (1)
- Hackensack, NJ (1)
- Hardyston, NJ (1)
- Hasbrouck Heights, NJ (2)
- Hawthorne, NJ (37)
- Highland Park, NJ (1)
- Ho-Ho-Kus, NJ (1)
- Jefferson, NJ (25)
- Jersey City, NJ (1)
- Kearny, NJ (1)
- Kinnelon, NJ (3)
- Little Falls, NJ (2)
- Long Hill, NJ (1)
- Lyndhurst, NJ (1)
- Mahwah, NJ (10)
- Manchester Township, NJ (2)
- Maplewood, NJ (1)
- Maywood, NJ (3)
- Mendham Township, NJ (1)
- Montclair, NJ (4)
- Montville, NJ (3)
- Morris Plains, NJ (1)
- New Milford, NJ (3)
- North Bergen, NJ (1)
- North Haledon, NJ (2)
- Oakland, NJ (3)
- Old Tappan, NJ (1)
- Oradell, NJ (1)
- Paramus, NJ (2)
- Parsippany-Troy Hills, NJ (1)
- Paterson, NJ (6)
- Pequannock Township, NJ (2)
- Ramsey, NJ (1)
- Ridgewood, NJ (14)
- River Edge, NJ (2)
- River Vale, NJ (3)
- Riverdale, NJ (2)
- Rochelle Park, NJ (1)
- Rockaway, NJ (2)
- Rockaway Township, NJ (2)
- Saddle River, NJ (3)
- Seaside Heights, NJ (2)
- Sparta, NJ (4)
- Sparta Township, NJ (3)
- Stanhope, NJ (1)
- Summit, NJ (2)
- Teaneck, NJ (4)
- Toms River, NJ (3)
- Vernon Township, NJ (2)
- Waldwick, NJ (1)
- Wanaque, NJ (2)
- Wantage, NJ (1)
- Wayne, NJ (13)
- West Milford, NJ (5)
- Wharton, NJ (1)
- Woodland Park, NJ (2)
- Wood-Ridge, NJ (1)
- Wyckoff, NJ (8)
Job Locations and Reviews


Arrived onsite for nitrogen leak test. Found leak outside in condenser near the refrigerant filter device. Possible other leaks outside but was not able to confirm. Inside found multiple leaks in the inside heat transfer media. Homeowner elected to replace AC system. Note the doorway will have to remove molding. New cabinet size is 17.5


Arrived for no cooling. Checked pressures at condenser. Condenser has 0 refrigerant. Checked filter. Unit has had no filter for a while. Customers interested in a leak test for unit. Made sure gates are closed before leaving. Customer acknowledged status of unit and signed off.


Arrived for diagnostic. Evaporator coils was all frozen. Whole Suction line was frozen. Turned off ac, turn on fan from auto, left site for ice to defrost. -came back to finish diagnostic. Unit was low on charge. Informed customer about unit status before charge. Customer approved charge up to 3 pounds on unit. Charged unit up to 3 pounds of Refrigerant, delta t jumped from 1 to 16 degrees. Unit has a fixed piston as a Metering device. Unit information after charge:


Arrived for Diagnostic. Both units are R22. 2 air handlers in attic. Both condensers run normally. Pressures for both condensers are low. First floor is low, upstairs is practically empty. Condensation pan for first floor was almost full from ice build up in the evaporator coil. Informed customer of units conditions. Customer is interested in replacing both units. Also wants to become a EPP member.


•Greeted customer upon arrival. •Customer lead me to air handlers. •Changed polarized filters for all 4 units. •Installed UV reflectors on all 4 units. •Turned on UV for all units. •Customer turned cooling on all 4 units. •All condenser turned on normally. •Cleaned all condensers with water and chemical. •Took pressures of all 4 condensers, all but one pressures were fine, outdoor temp was 64°F. •second floor condenser seemed to be low on refrigerant, informed customer, customer did not want recharge. •informed customer about all status and information of all units, Customer acknowledged and signed off.


Arrived onsite for ac maintenance on 4 systems. Turn AC on to confirm operation. Checked all electrical. Chemically Cleaned outside coils.


Arrived onsite for no cooling service call. Performed diagnostic and found system about 70% low in 410a. System take over 13 pounds of refrigerant. Observed air handler and found green solution on the air handler part indicating a significant refrigerant leak or dye escaping the system.


Found 75 gallon Bradford White water heater. Leaking tank was under warranty. Went to universal swapped out 75 gallon tank installed new 75 gallon water heater. Charging just labor rates.


created customer upon arrival. customer led me to basement for the unit was at. then led me around back to where the condenser was at. I then proceeded to change the filter of the unit. turned on all three thermostats to cooling. went outside saw condenser working / running. pulled the disconnect to shut condenser off. took off the top of the condenser. scooped off every dirt leaves branches and rocks from the condenser. clean condenser with water and chemical. put the condenser back together. open the electrical panel to check for high voltage low voltage and amps. everything seem fine. hooked up my field pieces to the condenser for pressure check, everything was fine. went inside with temperature probes put one in the supply duct and one in the return duct of the unit. delta(temp difference) reached 25°F. put all thermostats back to regular temperature 73° f. before leaving made sure everything was running and plugged in properly

Customer taking advantage of dryer vent special. Vent is clear and reattached. Secured with foil tape. Recommend upgrading to flex dryer vent with adapter for the wall vent to properly fit the dryer.


Customer taking advantage of dryer vent special. Found the dryer vent hard ducted. It was barely attached to the wall. Lint behind the dryer and near the failed connection at the wall. Cleaned out significant amount of lint. Blew 450cfm of air through the vent system. Vacuumed the floor behind washer and dryer and under the sink. Vent is clear and reattached. Secured with foil tape. Recommend upgrading to flex dryer vent with adapter for the wall vent to properly fit the dryer.

Arrived onsite for a no heat service call on master bedroom system. Performed diagnostic on system. Found a loose wire connecting the outdoor system to the indoor system. Reattached wire and system began cooling. Refrigerant levels 410a seem good.
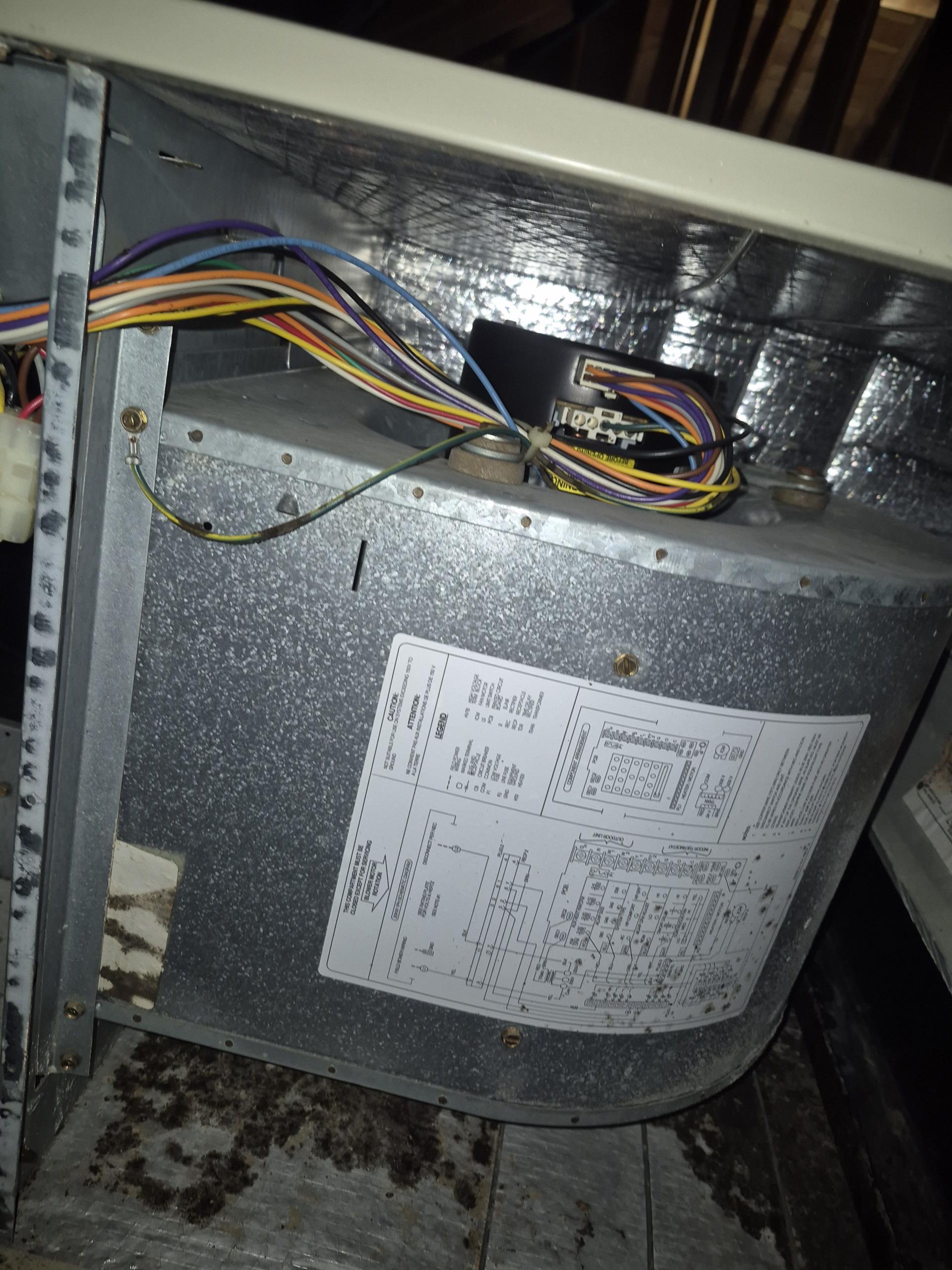

Arrived onsite to clean ac systems to remove organic growth and ad Indoor Air Quality solution to scrub the air. Opened all indoor air handlers. Removed blower fan cage from compartment. Used evaporator cleaners and cleaned entire inside compartment of each air handlers. Sprayed each evaporator coils. Removed any dust from the evaporator coils. We will return to add heat shield to the UV light system. To protect plastic flex ductwork, switch the UV light off for the moment.


Arrived onsite for issues with heating system. Homeowner is hearing the boiler click on and off constantly. Performed diagnostic. Had all thermostat turned on. Confirmed operation of the boiler. Confirmed operation of each zone. Boiler turned fired up and shut down at 180 degrees as designed and then came back on at 160 degrees as designed. All zone heated. All baseboard heated. Concluded that second floor bedrooms above garage may have had a frozen pipe stopping the flow of water. Homeowner will continue to observe that zone. Note the water heater is not providing the same about if hot water as it did in the past. Noted during maintenance they the water heater is past the age of replacement and should be replaced. Recommend on demand water heating system. Also, discussed the renovation to the shore house. Recommend adding in demand water heater there and recommend upgrading to heat pump system.


Arrived onsite for maintenance for one gas fired boiler. turned the thermostats up to heat and confirmed operation of the boiler and each zone valve. Turned the boiler off and removed and cleaned all burners and wiped cleaner the burner compartment. Performed a visual inspection of all electrical and inspected all external water components such as the exp tank, fill valve, backflow preventer and the circulator pump. Completed combustion test. At customer’s request installed 4 digital thermostats. Confirmed proper operation of all thermostats.


Arrived onsite to install gas shut off isolation valve behind clothing dryer. This is needed so homeowner can have their new dryer installed.


Arrived onsite to install gas shut off isolation valve behind clothing dryer. This is needed so homeowner can have their new dryer installed.


Arrived onsite for maintenance for one gas fired boiler. Turn on the thermostats up to heat and confirm operation of the boiler and each zone valve. Only found one zone valve but it was operational. Turned the boiler off and removed and cleaned all burners and wiped cleaner the burner compartment. Performed a visual inspection of all electrical and inspected all external water components such as the exp tank, fill valve, backflow preventer and the circulator pump. System working as it should. Performed dryer vent cleaning. Replaced 2 air scrubber bulbs by Argus. Please note 75 gallon water heater is due for replacement. It is manufactured in 2010. At 14 years old it is near failure which could be leaking and flooding the basement.


Arrived onsite for heating maintenance 4 gas fired furnaces with 2 humidifiers. Turned on all thermostats and Confirmed operation of all heating systems Basement Furnace Left: Turned on humidifier and set to winter. Panel 45 in good shape. Brushed and Wiped down furnace blower cabinet and gas burners. Burners fired and are in good working order. No visual impingement detected. Checked electrical. Cleaned flame rectification system. Measured 50 degree heat rise. System is operating as it should. Basement Furnace Right: turned on humidifier and set to winter. Panel 45 in good shape. Brushed and Wiped down furnace blower cabinet and gas burners. Burners fired and are in good working order. No visual impingement detected. Checked electrical. Cleaned flame rectification system. Measured 47 degree heat rise. System is operating as it should.


Installed new Aprilaire E100 Dehumidifier. Removed failed dehumidifier. Installed new dehumidifier. Connected thermostat controls for external blower motor. Connected ductwork and leveled system. Installed new custom drain pain. Reattached condensate drain line.


Arrived onsite for maintenance for one gas fired boiler. Requested the customer turn on the thermostats up to heat and confirm operation of the boiler and each zone valve. Turned the boiler off and removed and cleaned all burners and wiped cleaner the burner compartment: performed a visual inspection of all electrical and inspected all external water components such as the exp tank, fill valve, backflow preventer and the circulator pump. System working as it should.


Basement Furnace System: Turned on the heat and confirmed proper operation. Replaced the 20x25x1 filter and cleaned the blower cabinet and gas burners, which were in good working order with no signs of impingement. Blew out the condensate line for the condensing furnace. Checked electrical components, cleaned the flame sensor, and measured a temperature rise of 52 degrees (73/125). System is functioning properly. The filter cabinet is an older Lennox model with UV light bulbs. Recommended updating it for easier filter changes, but the homeowner is not interested at this time. Also noted that the humidifier is non-operational and suggested replacing it if dry air becomes an issue.
We’re thrilled to hear you were happy with our dehumidifier service in Franklin Lakes. The entire Climate Plus team takes pride in providing efficient and reliable solutions to keep your home comfortable. We look forward to assisting you again in the future!


Experience the comfort club difference with our After 2pm Arrival service! Our satisfied customer raves about our prompt attention to her dehumidifier issue, showing E4: NEEDS SERVICE. Trust us to keep your home humidity levels in check. Contact us today for expert service at competitive rates.

Experience a seamless 3C EPP late morning/ early afternoon arrival for organic growth assessment. Address cooling issues while alleviating headaches and coughing symptoms. No job notes from last maintenance visit. Contact us today for specialized service under Sheila Scherl's account.

Late Morning, early afternoon Arrival.
Fast and Friendly service!
Hi Michael. Glad we were able to provide you with the prompt and friendly service that you deserve. -Joe
Easy to Work With!